Understanding the Factors That Impact Pricing in Commercial Concrete Work
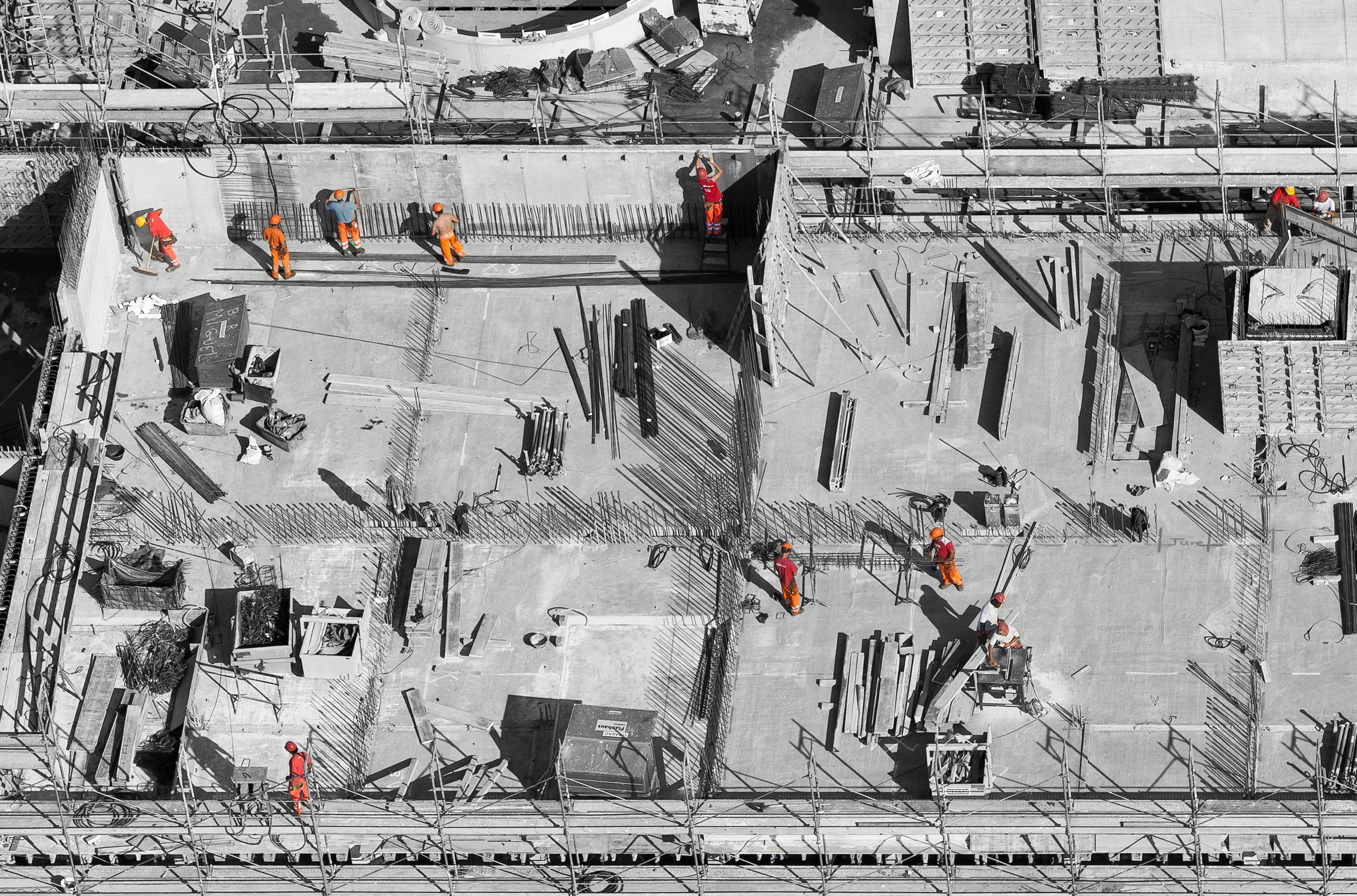
When it comes to commercial concrete work, one of the most common questions we get at Meyer Construction is: "What factors influence the pricing?" While concrete may seem like a straightforward material, the reality is that many variables play a role in determining the cost of a commercial concrete project. From the type of materials used to labor demands and logistical challenges, pricing is a complex equation that requires careful consideration. Let’s break it down.
Material Costs: The Foundation of Pricing
The materials used in commercial concrete work represent a significant portion of the overall cost. The price of cement, aggregates, and other mix components can fluctuate based on market conditions, such as supply chain disruptions or demand surges. For example, during peak construction seasons, the cost of cement may rise due to increased demand, directly impacting project budgets. Additionally, the type of concrete required for a project can affect pricing. Specialty concretes, such as high-strength or quick-curing mixes, typically cost more than standard concrete but may be necessary for projects with specific performance requirements.
Labor: The Skill Behind the Structure
Labor is another critical factor in pricing commercial concrete work. The complexity of a project determines the level of expertise and time required to complete it. For instance, pouring a simple slab may require fewer labor hours and less specialized skill compared to constructing complex architectural features or reinforced concrete structures. Additionally, labor costs can vary regionally and depend on the availability of skilled workers. At Meyer Construction, we prioritize hiring experienced teams who understand the intricacies of commercial projects, ensuring quality results while balancing labor costs.
Project Size and Scope: More Than Meets the Eye
The size and scope of a commercial concrete project significantly impact costs. Larger projects generally require more materials, equipment, and labor hours, increasing the overall expense. However, larger-scale projects may also benefit from economies of scale, potentially lowering the per-unit cost of materials or labor. Conversely, smaller or highly detailed projects, such as custom sidewalks or decorative concrete elements, may have higher costs due to the specialized attention required. A recent example from our portfolio involved a multi-level parking structure, where the scale allowed for efficient material ordering but required meticulous planning for reinforcement and curing.
Site Conditions: Working With What’s There
Every construction site presents its own unique challenges, which can influence the cost of concrete work. For example, a project on uneven terrain may require extensive site preparation, such as grading or soil stabilization, before concrete work can begin. Urban sites with limited space for staging materials or equipment can also drive up costs, as they require creative logistics and additional labor. Weather conditions are another factor that can affect costs. Pouring concrete in extreme temperatures, whether hot or cold, often requires special techniques and additives to ensure the integrity of the material, adding to the expense.
Equipment and Technology: Tools of the Trade
The equipment needed for a commercial concrete project also affects pricing. Depending on the project, specialized machinery like concrete pumps, laser screeds, or finishing tools may be required. While these tools increase efficiency and improve the quality of the final product, they can also contribute to the cost. Advances in construction technology, such as 3D laser scanning for layout or advanced curing methods, may also be incorporated to enhance project outcomes but may add to the budget.
Permits and Compliance: Ensuring Everything’s Above Board
Regulatory requirements and permits are often overlooked but are essential components of commercial concrete pricing. Depending on the project location, businesses must comply with local building codes, safety standards, and environmental regulations, all of which can add to the cost. For example, projects in areas with strict stormwater management requirements may necessitate additional measures like permeable concrete or runoff containment systems.
Timeline and Schedule: The Cost of Speed
The project timeline can also impact costs. A shorter schedule may require additional labor shifts, faster-curing concrete mixes, or premium charges for expedited material delivery. Conversely, longer timelines may reduce immediate costs but could lead to higher indirect expenses, such as prolonged equipment rentals or extended site supervision. Balancing time and budget is a critical consideration in every project we undertake.
Striking the Right Balance
At Meyer Construction, we believe in transparency and collaboration when it comes to pricing. By breaking down the factors that impact costs, we work with clients to create accurate estimates that align with their project goals. Whether it’s a large-scale commercial development or a smaller, detailed project, understanding these factors helps set realistic expectations and ensures the successful completion of the job.
If you’re planning a commercial concrete project, contact us today to discuss your vision. Our experienced team is here to provide guidance, create a tailored plan, and deliver quality results on time and within budget. Let’s build something incredible together!